风扇升降支架分模线错位的解决方案(风扇升降支架分模线错位的解决方案及原理)
作者:王 晨,李 强,康 雷 (广东省佛山市顺德区郑敬诒职业技术学校)文章已刊载在《模具制造》月刊,版权归作者所有,转载请注明出处,谢谢!
【摘要】介绍了落地风扇升降支架塑胶件分模线发生错位的原因,对定模型腔与动模型芯分型夹口易发生圆角、错位的问题作了分析,并通过改善模具制造工艺来解决该问题。
关键词:风扇;支架;分模线;型腔;型芯;模具制造
1 引言
2014 年 7 月,受某模具厂邀请,到厂检查落地风扇升降支架塑胶件缺陷。缺陷是塑件分模线有错位现象如图 1、图 2 所示。造成错位现象的主原因是模具型腔精加工、抛光等工艺不太合理。原设计是没有考虑到抛光会带来一些人为问题,主要表现在抛光时很难控制夹口位置,要么抛不到要求的光洁度,抛到要求的光洁度夹口处又有小圆角,两种情况都会给塑件外观带来缺陷,涉及到外观问题是绝对不允许的。但按工程师的思路反复的整改和维修后均无法彻底的解决此问题。通过以前在工厂制造及设计模具中长期结累的经验,并对问题进行全面分析后,制定出一套方案并最终解决了问题。

图1 分模线错位(夹口)图
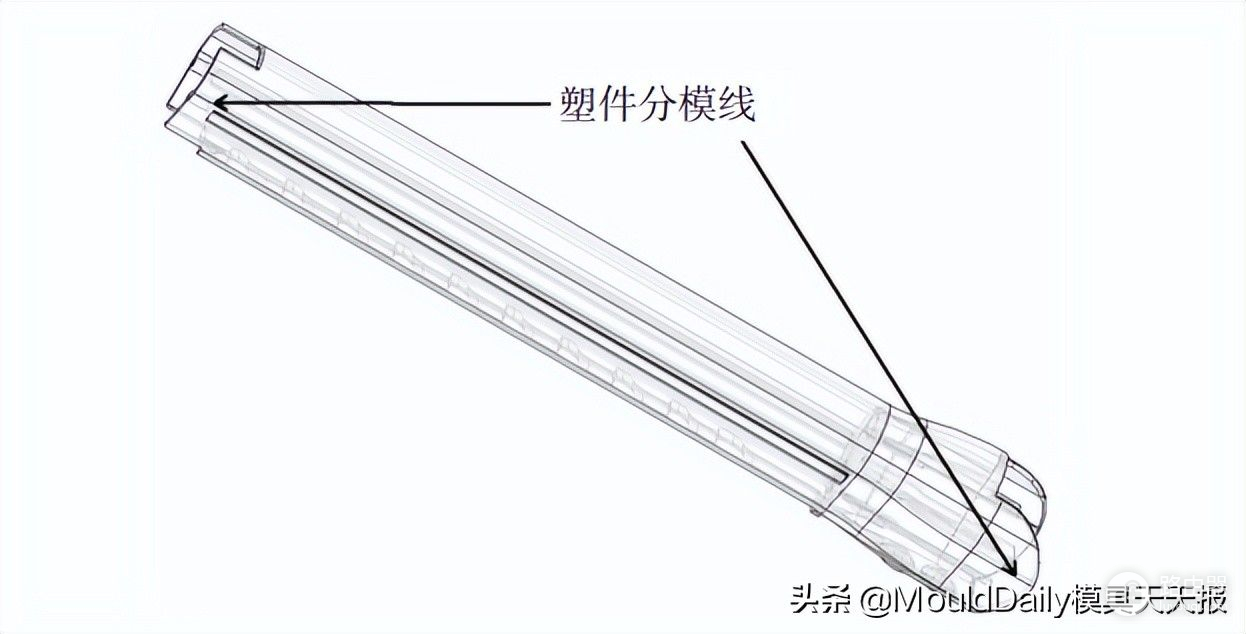
图2 塑件分模线图
2 存在的问题分析
2.1 塑件介绍
落地风扇升降支架塑胶件所用的是二烯-苯乙烯(ABS)料,外观表面拉光。塑件总高度为57mm,宽度为46mm,长度354mm(见图3),模具制造工艺如图4、 图5所示,先将塑件的两开口做两侧抽芯,再将圆弧和斜线相交出上下分模。

图3 塑件简图

图4 模具制造工艺图

图5 模具结构图
2.2 试产塑件问题描述
试模塑件及维修好几次的塑件都有错位现象,只是错位的大小不同,如图6所示,错位(夹口)有两种:①上小下大夹口;②上大下小夹口。

图6 错位(夹口)有两种
2.3 针对塑件出现的问题分析
(1)原注射模结构如图5所示,其设计、制造、成形工艺是:第一设计理念,采用点浇口,一模两腔,上下分型,左右抽芯,分型面及顶杆排气,定模型腔、动模型芯循环运水,抽芯后手动拿出塑件。第二制造工艺,依编程加工,定模型腔加工,动模型芯加工,面板加工,浇口板加工,定模板加工,动模板加工,顶杆面板、顶杆底板加工(同时加工)。第三成形工艺,把个零件组装好试模,用500t注塑机装模具,依照注塑参数进行注射塑件。
(2)从模具设计、模具制造工艺中出现了一些小纰漏。原因在于太理论化,疏忽机器精度和人工实操精度。定模型腔、动模型芯在某模具厂一次加工不能完全到位,要经过铣床加工,数控加工中心,雕刻机精雕,电火花加工才能完成。多次加工需多次装夹多次寻边,多道工序累积下来,累积公差就较大。特别在拋光时分模线很难控制,往往造成分模线上有小 R。这样积累下来定模型腔、动模型芯分模线不完全吻合,这时夹口就产生了,如图7所示。

图7 分模线错位
3 解决方案
3.1 传统的解决方案
(1)夹口、断差,设计师叫做分模线(分型线),形成原因有两种,一种是由于塑件结构的的原因引起,断差是由于分型面的高低不平所引起,塑件到设计师手里的时候,面本身是直身而且完整的面,由于分型面不平,需要同一个面一部分出前模,一部分出后模,所以这种断差是由于拔模斜度引起的。另外一种情况是由于在模具加工的各个环节中,都存在着加工误差,特别是对于非精密模具来说,多道工序累积下来,累积公差就比较大,最终塑件出来的时候,夹口就比较明显,需要修模师傅修夹口。
(2)钳工修夹口。
a.手工的方法。这种方法在以前加工设备落后,精度不高,成本太贵的情况下,使用较多,目前的加工工艺,尽量采用精密加工代替人工修复,但这种方法仍然是无法替代的。钳工师傅修模的时候先一面打上白漆,另一面打上红丹,修模之后就观察白漆面红丹印上去颜色的深浅程度,凭经验判断什么部位需要加胶多少,然后手工打磨,当然打磨的时候手感非常重要,这种打磨技术后期的钳工师傅可能赶不上早期的钳工师傅了,凭经验打磨得差不多了之后,重新装配好模具,再上啤机打样,塑件打出来后再观察夹口的修复程度,然后多次重复之前的工序,直到把夹口修到符合客户要求为止。
b.电极的方法。根据需要修夹口的位置,可以选择使用旧铜电极或者重新做铜电极,通过二次元或其它设备测量出夹口的平均值,然后平移铜电极或者碰数单边靠,偏心加胶来修夹口。对于要求比较高的塑件,可以采用立体铜电极(即整体铜电极),目的是尽量把外观和面积大的面整体一起放电,能很好的保证加工误差的一致性。立体铜电极跟普通铜电极不同之处在于5个方向都最好加工出来,普通的铜电极是3轴加工,立体铜电极可以5轴加工,也可以几个方向分开加工出一个整体铜电极。
3.2 制定新的加工工艺
(1)根据上面分析的结果及传统的解决方法,按现有的模具结构要用传统手工法来修复夹口问题几乎无法实现,原因是模具比较大装拆、打样耗时间耗物力且很难达到完全吻合。按第二电极的方法。可以修复分模线(夹口),但要花费很多时间及金钱,在小企业里利润薄的情况下是不会接受这种方法。所以必须寻找分析出产生问题的原因,设计出一种新的工艺结构,新的工艺是采用定模型腔、动模型芯分模线进行激光焊,在定模型腔、动模型芯设计加装拋光板进行加工,使定模型腔、动模型芯可以整体独立拋光。
(2)在原来结构上定模型腔、动模型芯设计加装拋光板,如图8所示。
(3)在动模型芯上设计加装拋光板,如图9所示。
(4)在定模型腔设计加装拋光板,如图10所示。

图8 拋光板

图9 动模型芯设计加装拋光板
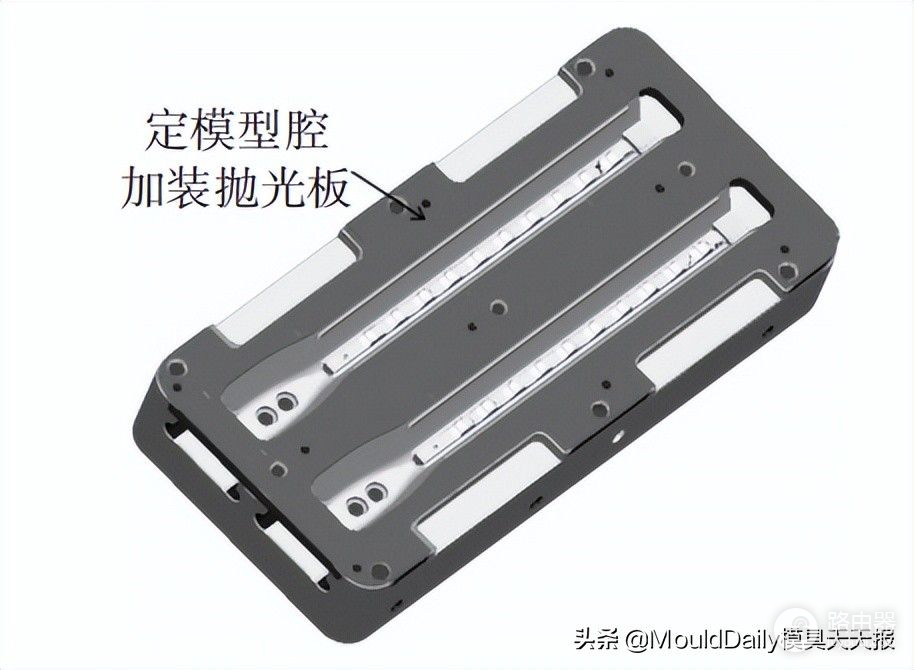
图10 定模型腔设计加装拋光板
(5)新工艺的优点。
a.在原来模具上进行添加一些工艺,这样可以节省材料。
b.整体模具的工艺不变,只是型腔上加装抛光板,利于装拆维修。
c.节省费用,提高效率。
(6)新工艺流程。
a.拆模→设计定模型腔、动模型芯及抛光板定位孔、螺丝孔→定模型腔、动模型芯钻定位孔、螺丝孔→依图制造抛光板→定模型腔、动模型芯分模线烧激光焊→磨平分型面→抛光板固定在定模型腔、动模型芯上→定模型腔、动模型芯在电脑加工中心锣型腔(连带抛光板)→定模型腔、动模型芯带抛光板抛光到600#砂纸→拆卸抛光板→定模型腔、动模型芯利用咬位固定好型腔→定模型腔、动模型芯吻合精修分模线(夹口)→拆开定模型腔、动模型芯各自装好抛光板→抛光到镜面→组装模具→试模(20PCS)→客户确认→交模具。
b.定模型腔、动模型芯分模线烧激光焊简视图,如 图11所示。

图11 动、定分模线烧激光焊简视图
烧激光焊时要注意画粗线部分往型腔焊接2mm左右,焊条材质与定模型腔、动模型芯材质一样。
c.制造定模型腔、动模型芯及抛光板定位孔、螺丝孔。
模具拆开后先测量动、定模型芯、型腔的外围尺寸→用CAD设计好定位销钉和螺丝孔→用Pro/E设计好抛光板→用国产718料制造抛光板,依设计图纸用立式铣床加工外围尺寸、销钉孔、螺丝避空(型腔孔不用加工)→抛光板两大平面用平面磨床磨两面→定模型腔、动模型芯用立式铣床校正后钻定位孔、螺丝孔。
d.定模型腔、动模型芯及抛光板用电脑加工中心加工。
动、定模型芯、型腔各自装上抛光板,用销钉定位、螺丝拧紧→上加工中心、校正、寻边(分中)→按照编程粗、精、铣削定模型腔、动模型芯及抛光板(特别注意动、定模分模线与抛光板型腔接顺),如图12所示。
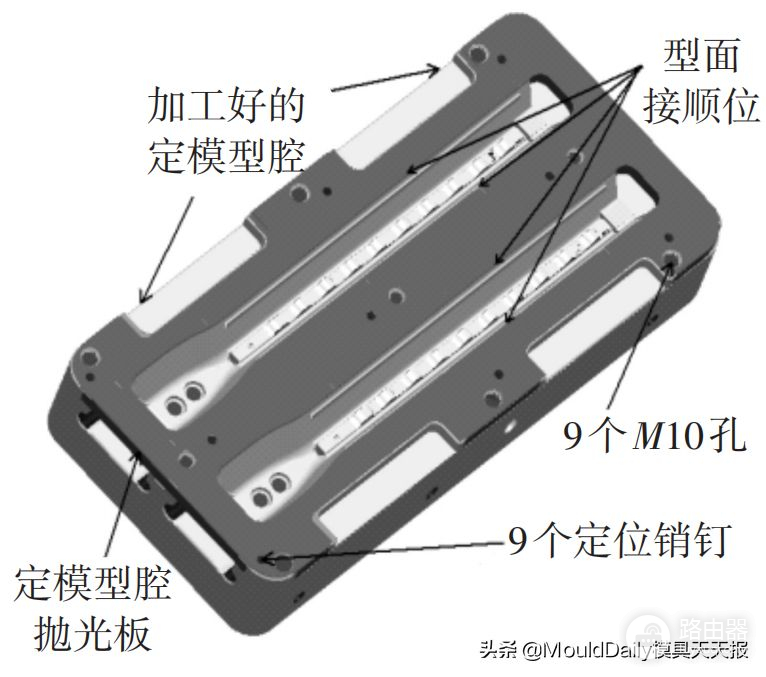
图12 定模示意图
(7)模具抛光。
型芯、型腔及抛光板CNC完成后→定模型腔、动模型芯分开抛光(抛光板不能拆)→抛光先用150#油石抛光到600#油石→用200#砂纸抛光到600#砂纸→拆开抛光板→合并定模型腔、动模型芯→精抛分模线位(夹口位置,见图13)→精抛光后,拆开动、定模→定模型腔、动模型芯各自装好抛光板→把型芯、型腔从粗到细抛到3#金相砂纸→用研磨膏把型腔抛光成镜面。

图13 精抛分模线位(夹口位置)
4 结束语
通过上述工艺的改良,解决了塑件的外观缺陷,并缩短模具制造周期。此工艺之后被某模具厂广泛地运用在同类型的模具结构上,解决了不少的技术问题。在以后的工作中自己还要不断的学习,不断的在工作中总结经验,将自己的技术水平再提高到新的高度,将来更好地为社会服务。
—The End—